Vandersanden disrupts the construction sector with carbon-absorbing brick
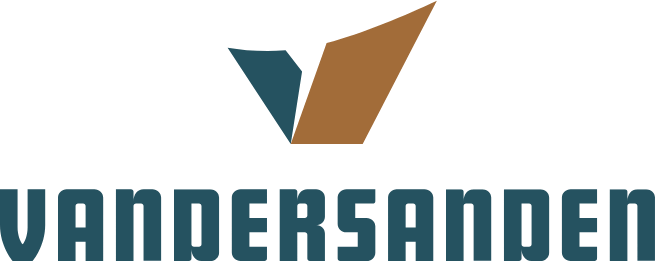
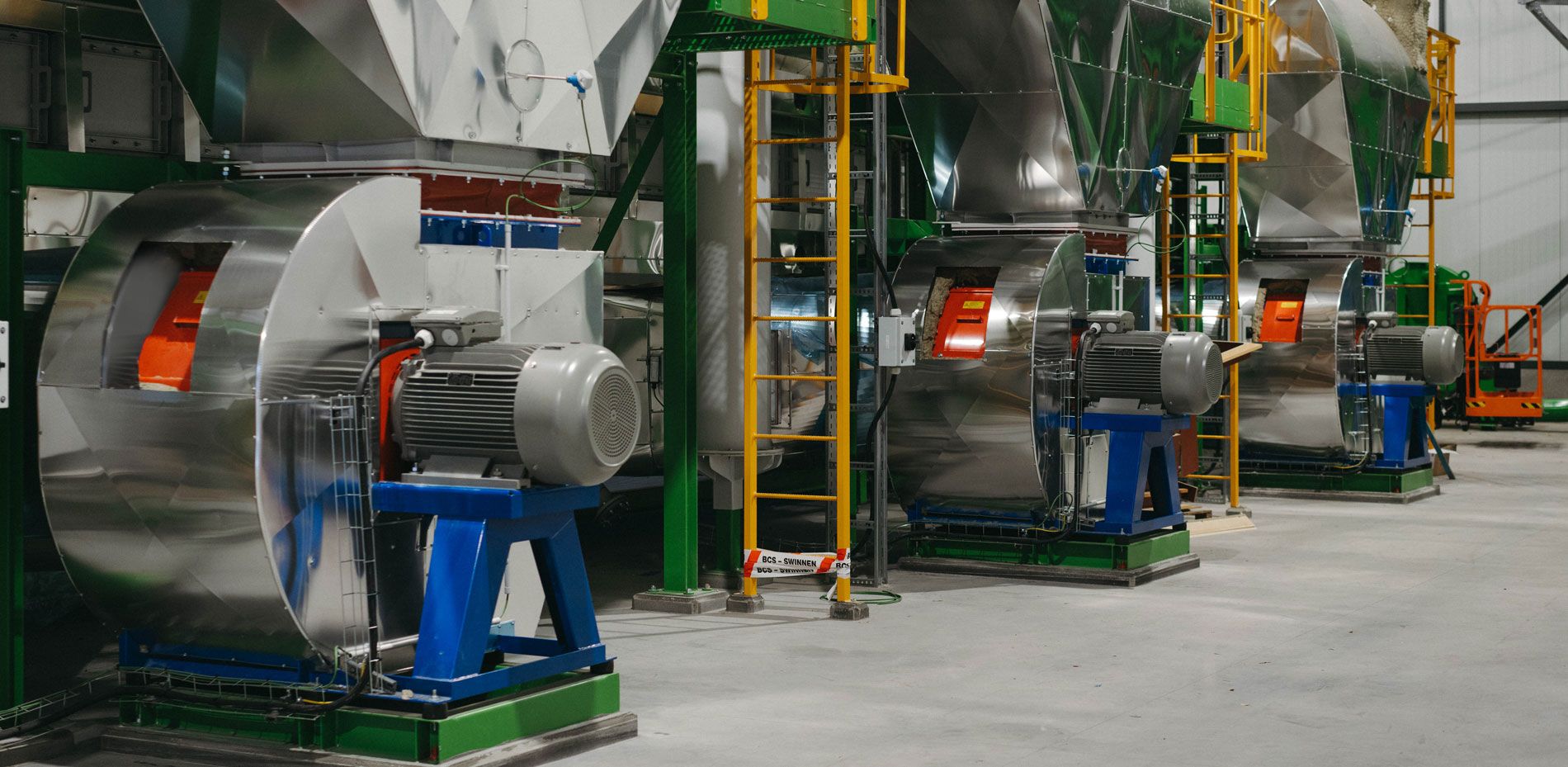
Vandersanden builds a new brick factory in Lanklaar, Belgium, using innovative cleantech designed by CEE.
- Scale: 200.000 metric tons/year
- Carbon absorption: 12.000 metric tons CO2 per year
- Fossil fuel elimination
- 80 % lower energy demand
- Energy Recovery
Redefining innovation with disruptive cleantech
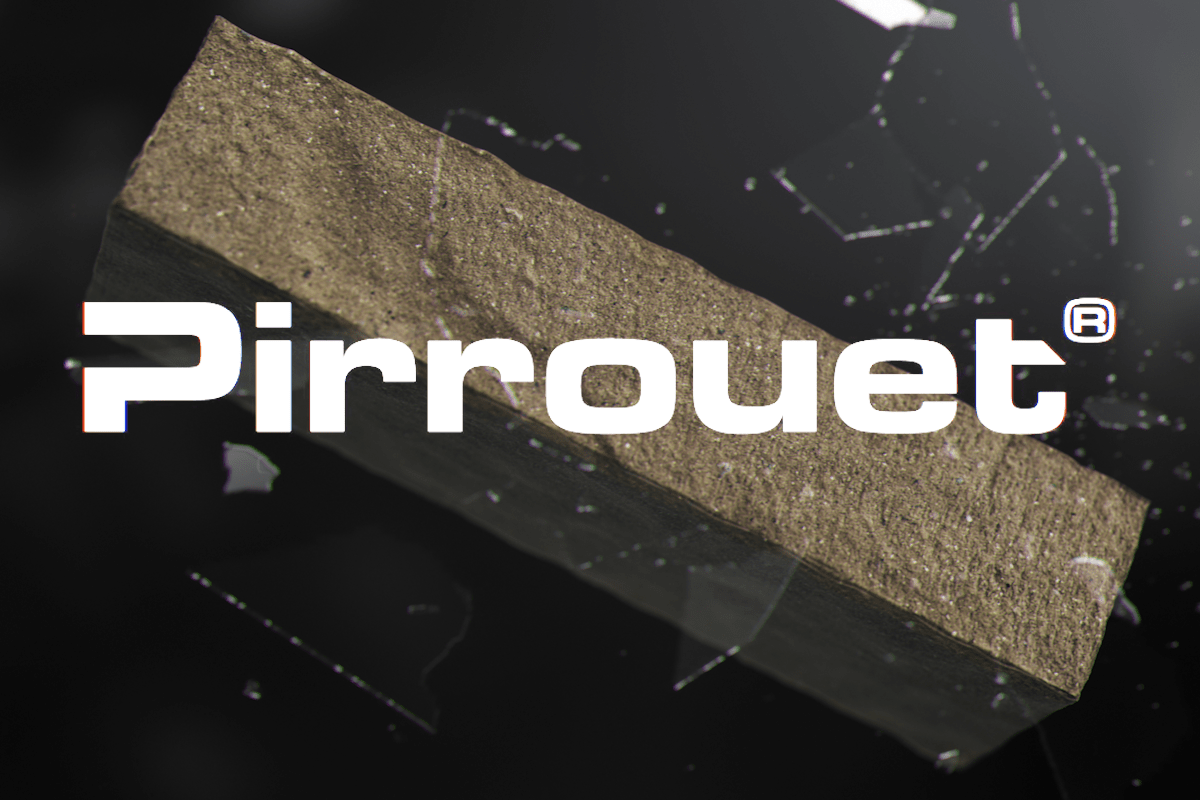
Reducing Greenhouse Gas (GHG) emissions is a top priority for industrial companies looking for ways to comply with sustainability legislation or corporate frameworks like the SBTi. Many energy-intensive and fossil-fuel-dependent industries are investigating alternative methods that allow them to transition to net zero. But why stop there?
Vandersanden, a Belgian brick producer, took it a step further. They enlisted CEE's cleantech expertise to build a new factory that produces a trail-blazing carbon-negative brick called Pirrouet®. By reducing carbon emissions and integrating sustainability into the entire production process, Vandersanden is making significant strides toward achieving at least CO2 neutrality by 2050.
The ingenuity of this case lies not only in the new approach to fossil fuel elimination and CO2 reduction. It is a prime example of disruptive innovation and new technology development. Together with CEE, Vandersanden challenged the status quo. A brand-new way of producing bricks emerged, skipping the traditional 'baking' or sintering phase and inventing another way of achieving the desired result.
CEE's secret weapon for this project? Our patented full-scale section lab, where we executed extensive pilot-scale tests. By combining our knowledge with the possibilities of our lab and smart simulations, we guarantee performance when scaling up new technology while simultaneously expediting the realization. Due to the technical complexity of this turnaround, we facilitated this transition by working with an ESCO contract.
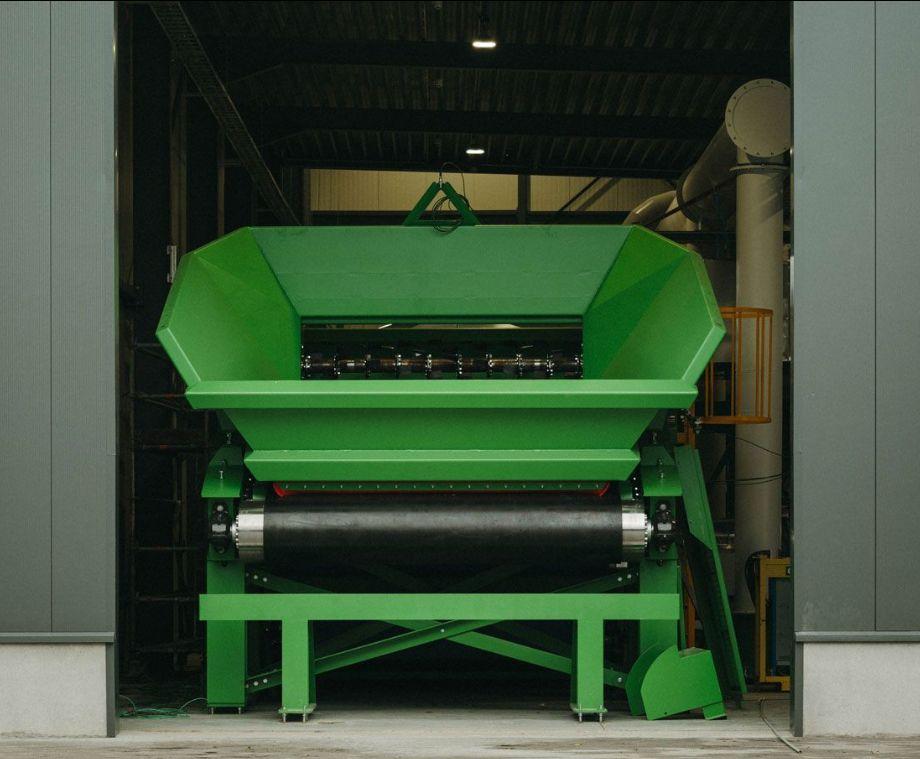
A 360° approach to reducing and reusing CO2
Traditional brick production processes rely on drying and high-temperature sintering to solidify the bricks. This is an energy-intensive, fossil-fuel-dependent process emitting tons of CO2 emissions. Upon Vandersanden's request, we went back to the drawing board. The result is an entirely new way of producing bricks, thanks to a process that bypasses the need for sintering and instead relies on innovative drying techniques. The emerging alternative tackles GHG emissions from different angles by thinking outside the box and re-examining traditional brick production processes. As a result, the bricks' production process is 100% fossil fuel-independent
"Vandersanden has set itself the objective to be fully carbon neutral by 2050. With this CO2-negative façade brick, we make a significant step towards this objective” - Rudi Peeters, former CEO of Vandersanden.
Long-term collaboration leads to lasting changes.
For almost two decades, CEE has supported Vandersanden in its quest for reduced energy consumption and CO2 emissions. Heat recovery and waste heat utilization, generating cold from heat using absorption cooling, super-heated steam drying, and making drying more sustainable using heat pumps are a few of the significant steps towards more sustainable processes that have been taken, and more are in the pipeline.
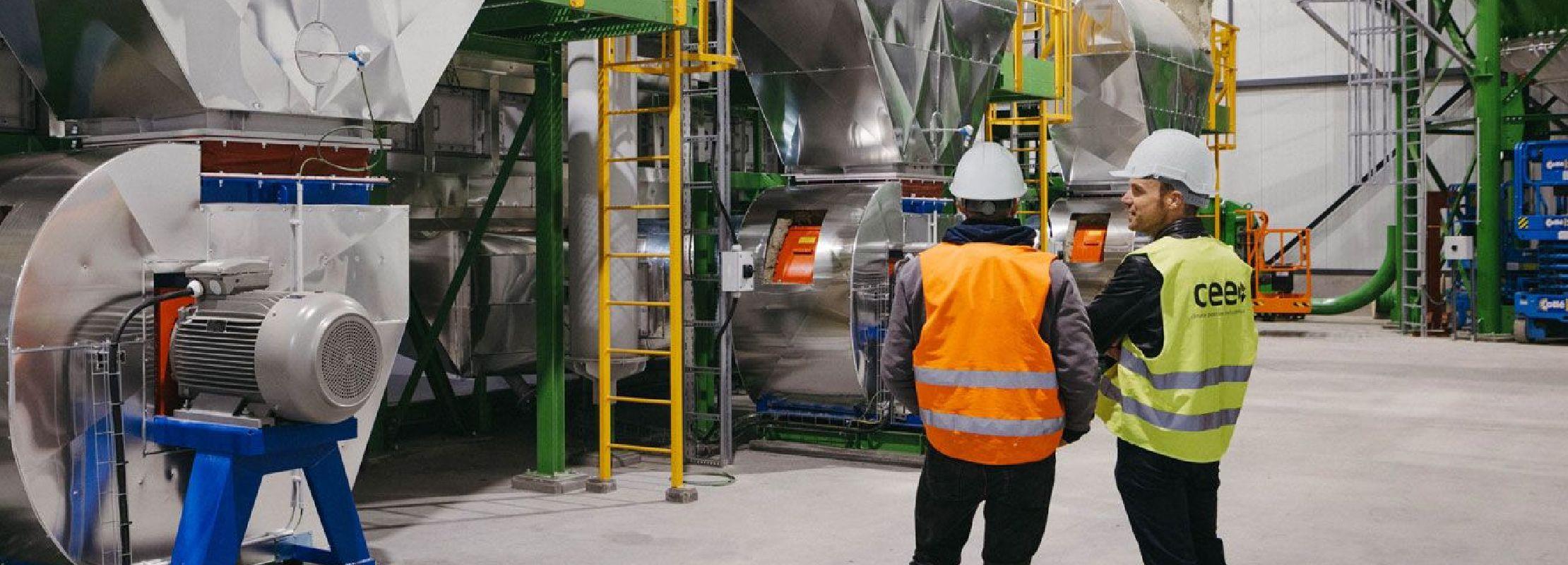
A comprehensive approach to innovating industries
Part of our strength lies in our versatility. As your partner, we don't stop at reducing your carbon emissions by optimizing your process's energy consumption. Our cleantech lends itself to vertical integration throughout your entire value chain. We accompany you on your entire innovation journey, from the conceptual phase until maintenance or exploitation once a new project runs. As demonstrated in the Vandersanden case, we excel at:
New technology development
Vandersanden had a fantastic idea: to create a carbon-negative brick. This is a truly revolutionary concept that will change the construction materials sector forever. We help our customers fulfill their missions. Thanks to our full-scale section lab, we converted their disruptive dream into a fully implemented process.
The carbonatation room, which absorbs carbon emissions from other sources, is key to the complete reversal of dealing with carbon emissions in this process. We built the pilot-scale carbonatation room, which laid the groundwork for the eventual large-scale version.
Reinventing drying technology
Thanks to the process's reinvention, Vandersanden no longer needs to rely on energy-intensive, inefficient drying. Instead, they have a new high-precision dryer that delivers a homogenous and precisely dried product, preparing for a high-quality carbonatation in the next phase of the process.
Energy recovery
Partnerships can take many forms. With an ESCO contract, we recuperate energy from existing product lines' flue gases. This is another way of introducing innovation and sustainability while alleviating Vandersanden from the burden of execution and associated risks.
Ready to re-invent industry standards with us?
Whether you have net zero ambitions or want to completely re-invent your production process, we are always open to exploring new possibilities together and resetting the standards for sustainable industrial practices!