ETEX and Promat install two super-heated steam dryers
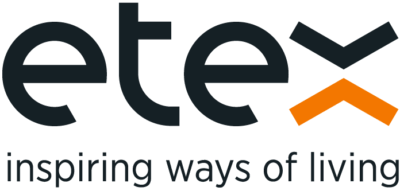
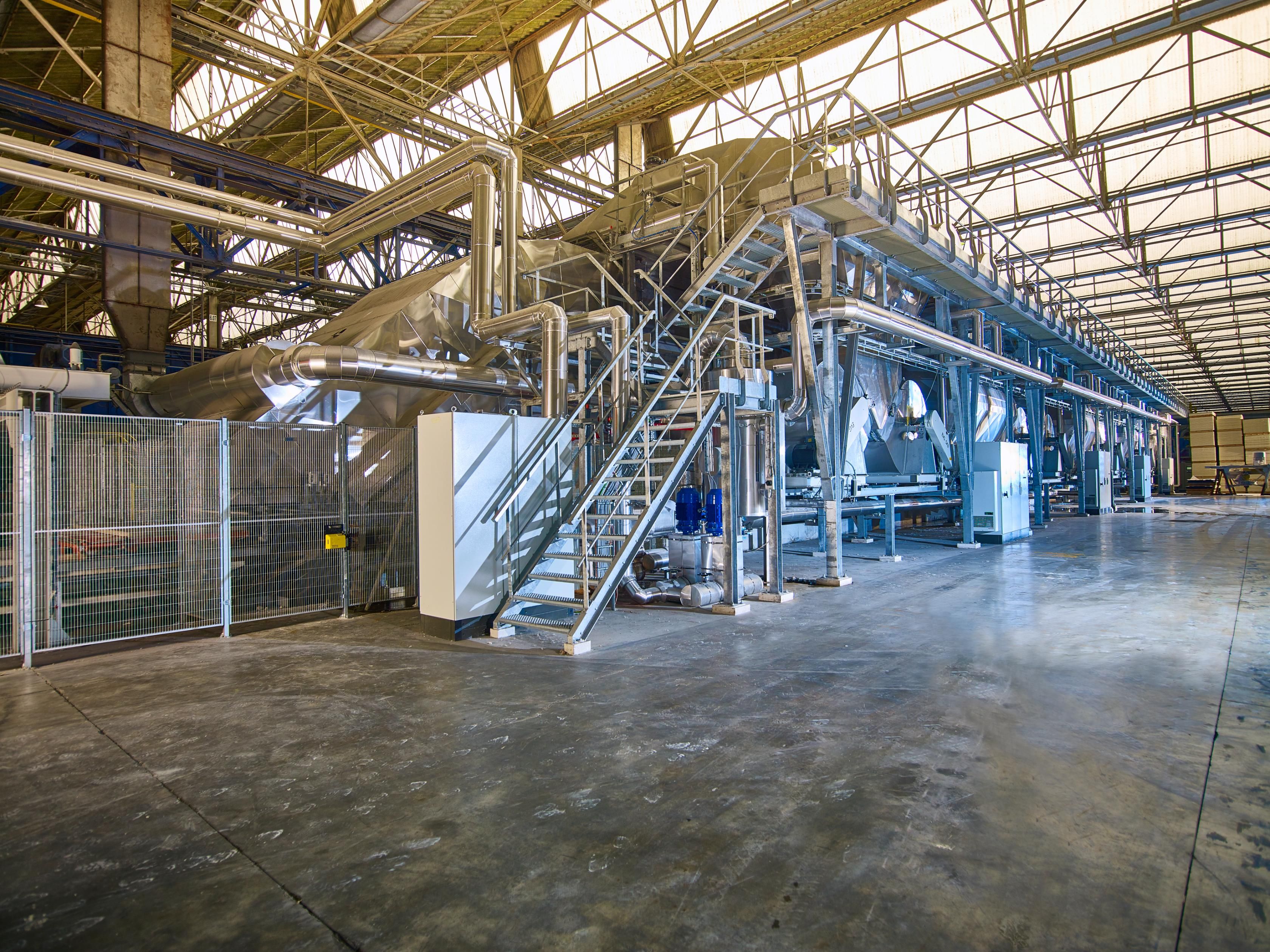
A long-term collaboration resulting in two steam drying lines at Promat, Tisselt
- High-precision control
- 20 to 50 % reduced energy consumption
- Heat treatment up to 5 MW
- Safe automated operation
- Smart electrification with heat pump
- 100% water recovery
Energy-efficient and hyper-precise drying of construction materials
Like many other industries, the building materials sector grapples with the balancing act between sustainability, technicality, and profitability. Due to its traditionally energy-intensive production processes, the industry's energy cost entails, on average, 20% of its total spending. The drying process, in particular, consumes a large part of this energy cost because large quantities of water need to evaporate. Drying technology needs to be hyper-precise to reach the right moisture level in the end product, which is critical for construction materials such as bricks or fire-resistant panels. On top of that, the sector cannot escape the trend toward decarbonization. Finally, the nature of drying implies high temperatures; therefore, a safe production process is paramount.
In search of an innovative solution, Promat and ETEX called upon CEE. Promat is the Belgian fire-resistant building materials and high-temperature insulation division of ETEX, a group specializing in the production of building materials. In alignment with their ambitious decarbonization goals, the group collaborated with us to co-develop an innovative treatment and drying process in an atmosphere of 100% superheated steam (SHS). Thanks to our expertise and full-scale section lab, we expedited the transition from test to full-scale application in a four-month time span.
ETEX decarbonization goal: 35% reduction of greenhouse gas (GHG) emission intensity by 2030.
Promat produces up to 7 million m² of fire protection solutions yearly, such as fire-resistant building panels. Their drying process needs to meet the following criteria:
- Evaporation of up to 70kg of water per board or panel to a precise %
- Homogeneous drying across boards of 2m50 by 1m20
- Thicknesses from 20 to 85mm
- A capacity of 3 metric tons of water evaporation per hour
- Development and reproduction of an optimal drying recipe for quality and performance
The cleantech that we built around Promat's products is truly groundbreaking and exhibits impressive benefits:
- Unprecedented levels of precision, down to 1% tolerance on moisture level
- Reduction of energy consumption up to 50%
- Automated operation
- Potential of 100% decarbonization
- In support of ETEX' SBTi goals
- Continuous monitoring of performance and efficiency, with direct intervention by CEE for optimization
Specifically, CEE designed two large-scale super-heated steam dryer lines.
Key features of the new installation:
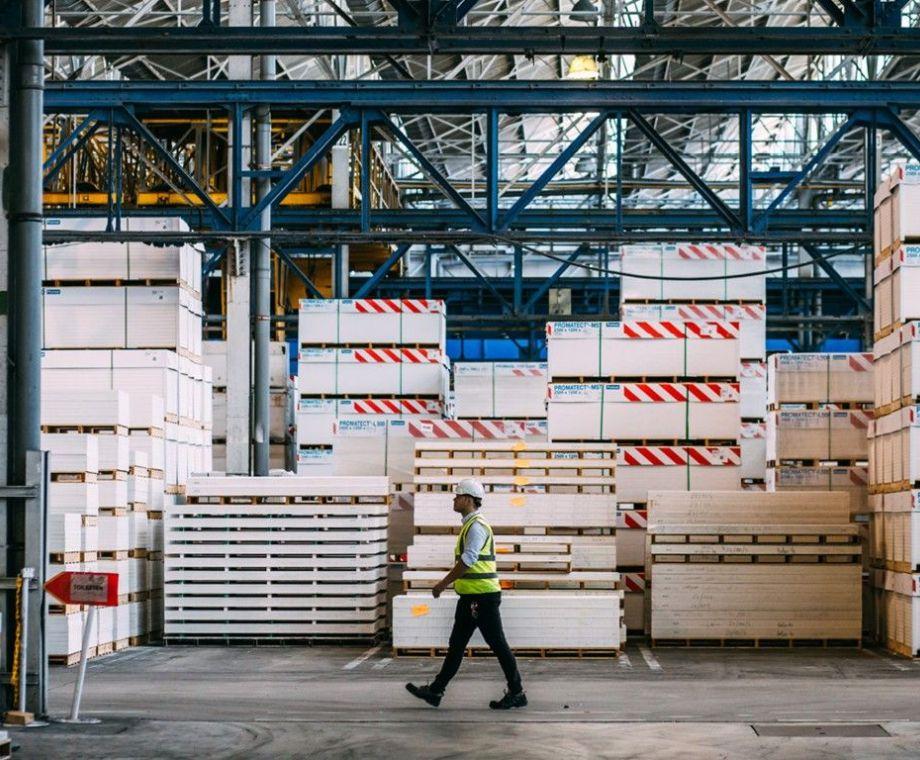
Line 1:
- High-precision control
- 20-50% lower energy consumption than conventional dryer
- Reduction of natural gas consumption by 30%
- Safe automated operation
- Capacity: 2,4 ton/h – footprint: 60m x 8m x 7m
Line 2
- High-precision control
- Smart electrification with integrated heat pumps
- 50% lower energy consumption
- 72% CO2 reduction, with the potential of evolving to 100% decarbonization
- Safe automated operation
- 100% water recovery
- Capacity: 2,4 ton/h – footprint: 52m x 7m x 7m
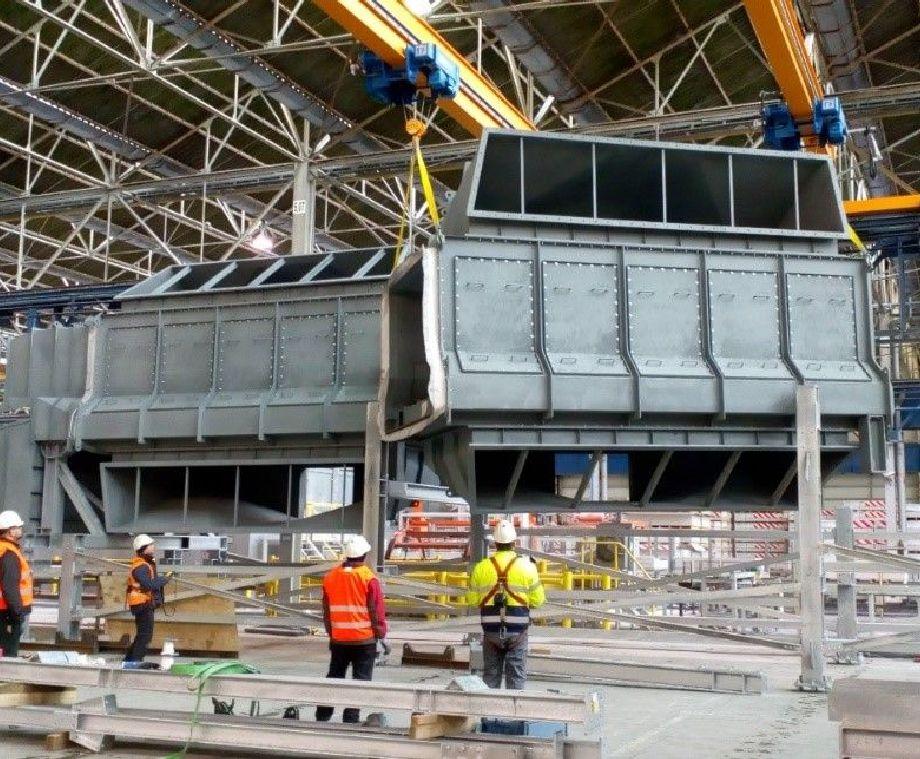
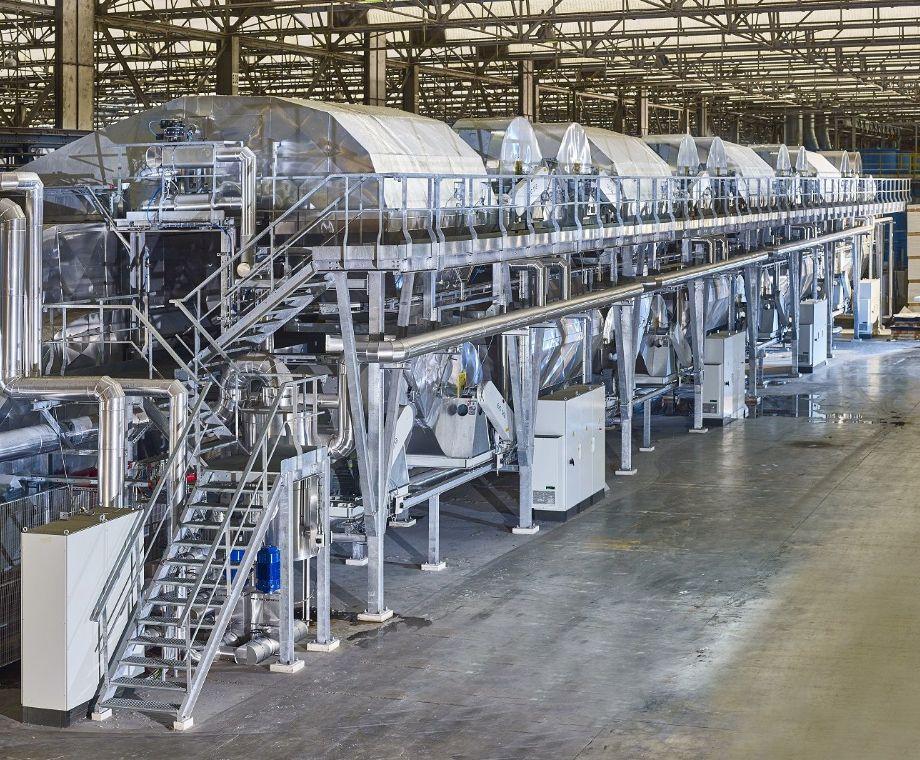
High precision
We built an SHS drying tunnel with eight separate drying zones. The temperatures, moisture content, and recirculation speed of every zone are controlled for precise reproduction of the recipe over the tunnel's length.
Our SHS treatment of fire protection construction materials is designed to preserve an exact quantity of moisture in the material. This feature significantly enhances the fire-resistant performance of the material, even in the most stringent conditions, providing a robust and safe final product.
Steam drying allows for better process control, more homogeneous results, and improved quality overall.
Energy-efficient
Many traditional industrial drying processes use air to extract moisture from the product. This is an energy-intensive method. The cooled and moist air is expelled, with, at best, some of the energy recovered to the air inlet. The dry air mass flow at exit temperature defines the heat losses and, thus, the energy consumed by the process.
By switching to SHS drying and reducing the use of fresh air significantly, CEE's solution reduces Promat's energy consumption by 20 to 50% compared to hot air drying. It also simplifies latent heat-recovery of the vapor produced. In combination with solutions like high-temperature heat pumps and mechanical vapor recompression (MVR), our technology can recover up to 95% of process energy. For the second drying line, in total, 900 kW of heat is recovered from the evaporated water and re-injected with 150 kW input to the heat pump.
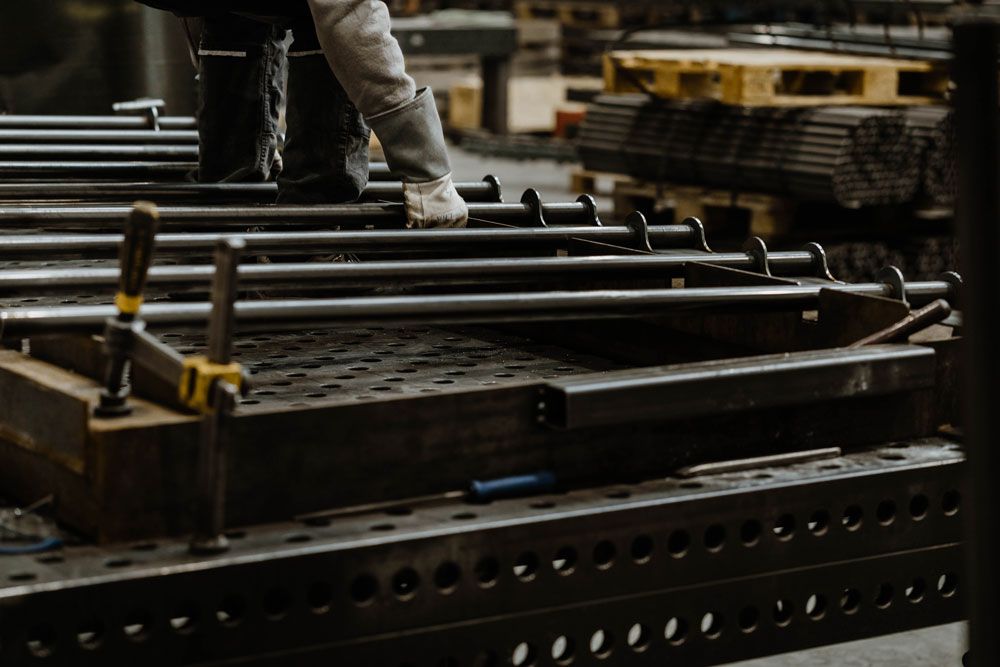
Decarbonization
This technology also allows for complete electrification thanks to the radical energy reduction by switching to steam-drying. Combined with renewable energy sources, it is an economically viable way to achieve 100% decarbonization in industrial drying processes. In other words, it's a highly effective and beneficial avenue towards net zero, not just for drying construction materials such as brick, gypsum blocks, or fiber cement panels, but also for industrial drying in other sectors such as the food and beverage industry.
Minimal downtime
The two drying lines' modular design enables maximum premanufacture off-site and reduced assembly time on-site. It also allows for easy maintenance, sustainable life-cycle management, and overall reduced downtime.
CEE developed and meticulously executed a preventative maintenance schedule. Since the startup and commissioning of the first line in 2018, there have been no unscheduled stops.
Ready to explore the infinite potential of super-heated steam drying in transforming your production process?
Together with you, we build the exact solution you need, tailored to your product.
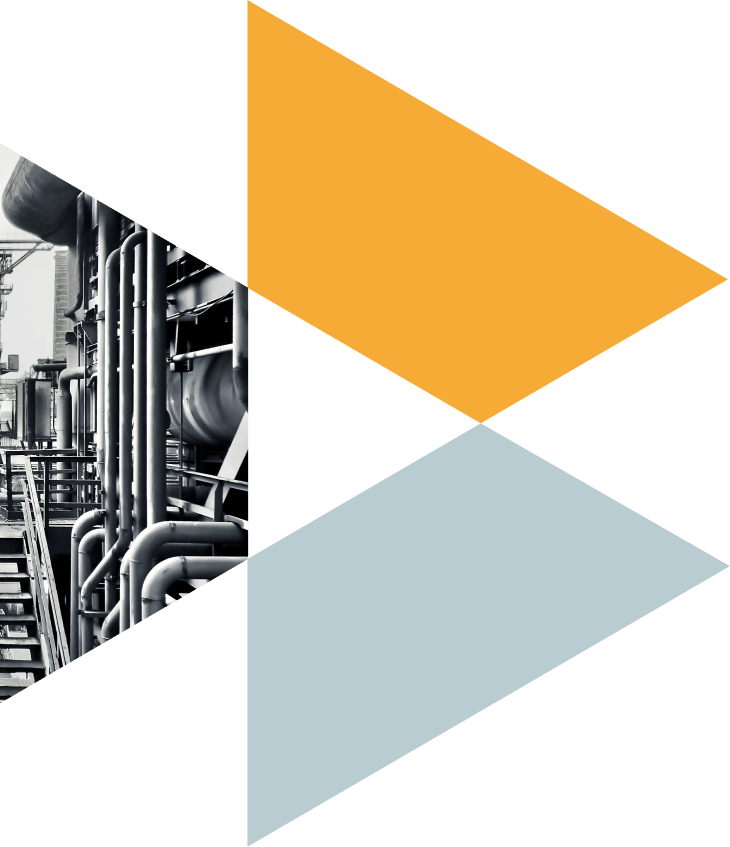