CEE accelerates Barry Callebaut's global net-zero transition

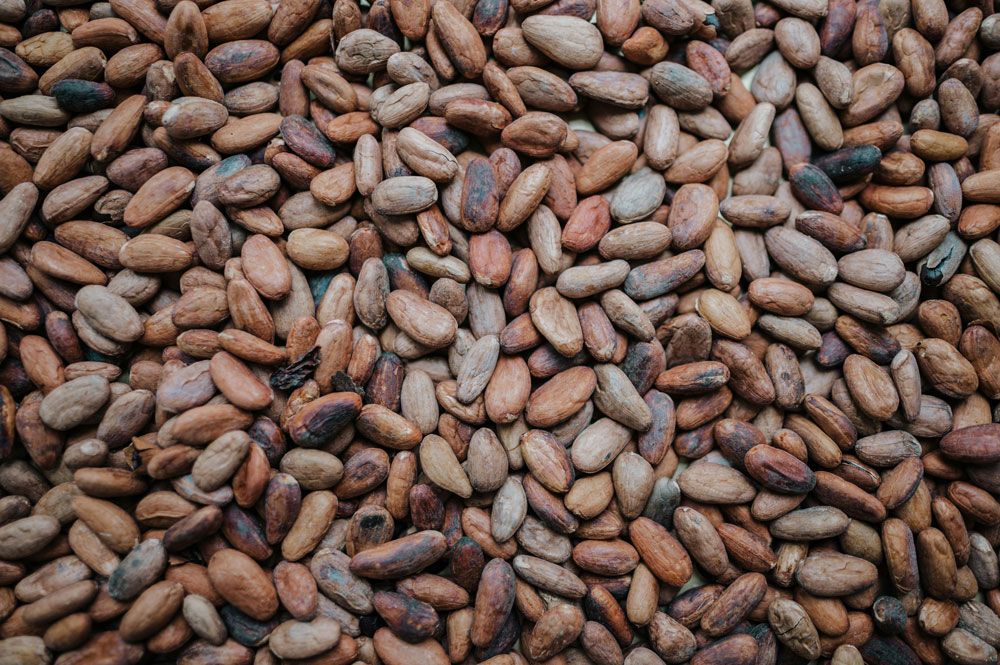
Improved energy efficiency and reduced carbon emissions at Barry Callebaut's Banbury plant in the UK:
-
Redesigned heat network
-
Heat pump efficiency x2
-
60% reduction in carbon emissions
-
The record-breaking success of this project was the turning point for an accelerated net-zero transition for Barry Callebaut worldwide
Reducing chocolate's carbon footprint with smarter heat and cold balancing
Heat and cooling are required for the production of chocolate. Hot water is used for heating, traditionally generated by decentralized natural gas-fired steam boilers. Cold water is used for cooling and is often supplied through traditional cooling machines. The efficiency of this process can be improved with heat & cold balancing.
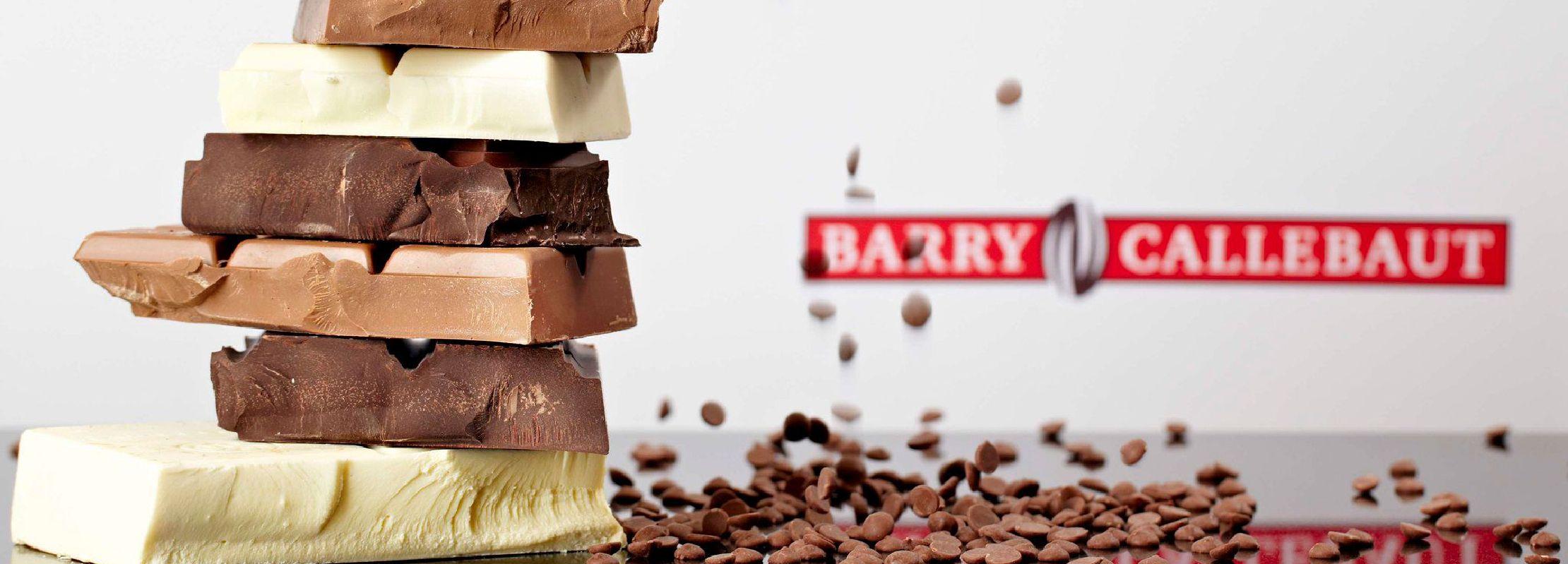
This is precisely what CEE accomplished for Barry Callebaut in Banbury. First, we redesigned the heat network with improved heat and cold balancing. Next, we installed an integrated production heat pump. We drastically improved the heat pump's effect by bringing the temperature levels of cooling and heating closer together. The results? Beyond impressive:
Increased energy efficiency: the heat pump COP (coefficient of performance) increased from 4 to 8
A 60% carbon emission reduction
Safeguarded thermal processes through adequate heat and cold buffering
Precision control through monitoring
Eliminated ozone impact and 0 Global Warming Potential (GWP) by switching to NH3 as a coolant
The record-breaking improvement in energy efficiency, combined with the drastic emission reduction, translated into a pivotal moment for Barry Callebaut. This project serves as an example of their global scope 1 and 2 decarbonization targets. Its success assured a smooth and accelerated transition to net zero, not only for the Banbury plant but also for others.
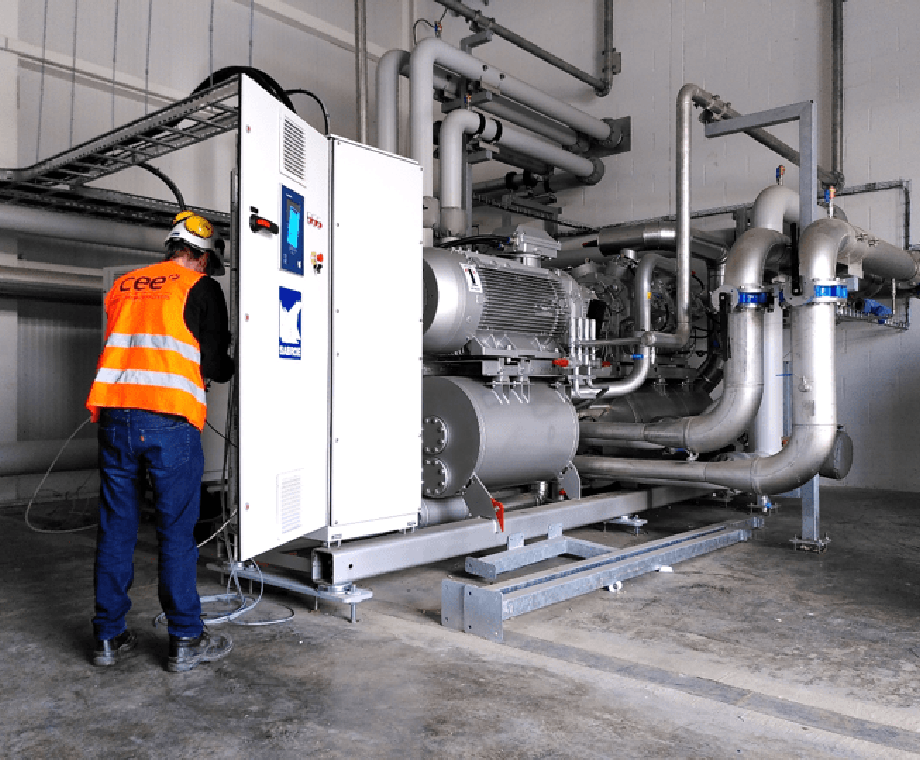
Technical details:
- Installed cooling capacity of +/- 2,5 MW through an NH3 heat pump, a NHR compressor chiller and adiabatic coolers
- Installed heating capacity of +/- 1MW through a NH3 heat pump
- Thermally layered buffer capacity with a total volume of 85m³ at various temperatures
- Distribution of heat and cold via +/- 1.5 km piping in stainless steel 304L in diameters varying between DN20 and DN200
- Full in-house electrical design and programming
The benefits of process-integrated optimization
Eliminate fossil fuels
In the past, industrial organizations often installed steam-powered networks that ran on fossil fuels. This was the traditional way of meeting heat and cold requirements, not just in the food industry. Increased awareness about the negative climate impact of fossil fuels initiated a global search for alternative production methods.
The starting point is smart integration and balancing of heat and cold flows. Utilizing electricity powered by renewable energy eliminates the need for fossil fuels, reduces carbon emissions, and meets SBTi targets.
Improve energy efficiency
After critically examining and redesigning Barry Callebaut's Heat Cold Network, we prepared the site for the energy-efficient installation of heat pumps. As a result, we allowed a smooth transition to the complete process of electrification.
The key benefit of this approach is an additional 50% reduction of energy costs on top of the heat pump COP. As a result, even with a significant cost spread between gas and electricity, switching to electricity with highly efficient heat pumps is beneficial. Also, the cost of fossil fuels and European Emission Allowances (EUA) will continue to rise, increasing the financial benefit of a heat pump investment.
For Barry Callebaut, adding the heat pump to their UK project had a payback of 4 years. As a result, they plan to add more heat pump capacity, which will cut almost all CO2 emissions from the UK site by 2025.
Precision control through comprehensive monitoring
Redesigning your heat network will increase the stability of your production process and achieve optimal energy performance. Targeted energy performance monitoring will ensure stable and safe operation. An abundance of sensors and pumps will ensure high reliability and availability of the hot and cold sources.
Ready to go net zero?
Are you a fellow front-runner in the transition to net zero? CEE's own facilities offer the chance to test together with industrial partners. If you want to explore future collaboration options, reach out to learn more!
Ready to go net zero?
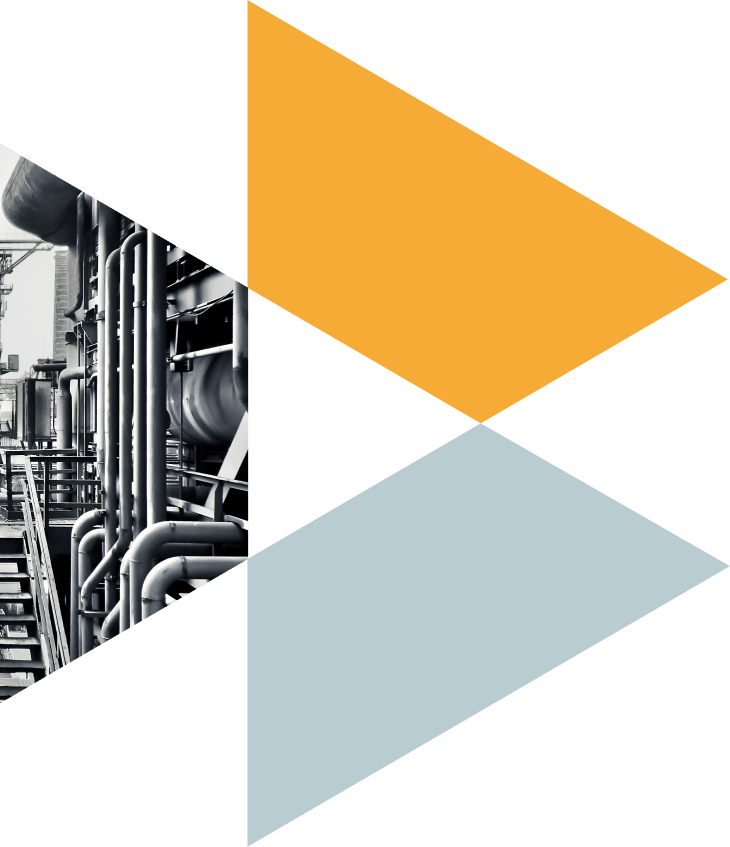